Side Feed Automatic Sleeve Sealer
The side feed sleeve sealer offers you enhanced flexibility in your operation, with the ability to run singles, multipacks, trayed or trayless items.
It provides total control and flexibility, making it ideal for contract packers and growing businesses.
Feeding products at a 90° angle to the shrink tunnel, the sealer employs a positive push action to easily collate items.
Changing between different orders or collations is simple with just a tweak of the settings.
A standard pack clamp ensures stability, even for stacked products.
Applications for Side Feed Automatic Sleeve Sealers

Aerosols

Multipacks

Collations

Food & Beverage

Bottles

Trayed Items

Jars

Personal Care
Key features
BAMA Compliant specification
Available for aerosol packaging applications.
Simple controls
For total ease of operation. Available as a HMI or switch-based system.
Adaptable infeed
To accept trayed and trayless wrapping applications.
Full perspex guarding
CE marked guarding guaranteeing operator safety but also full line of sight operation.
Low mounted film holder
For easy and safe loading of shrink film reels.
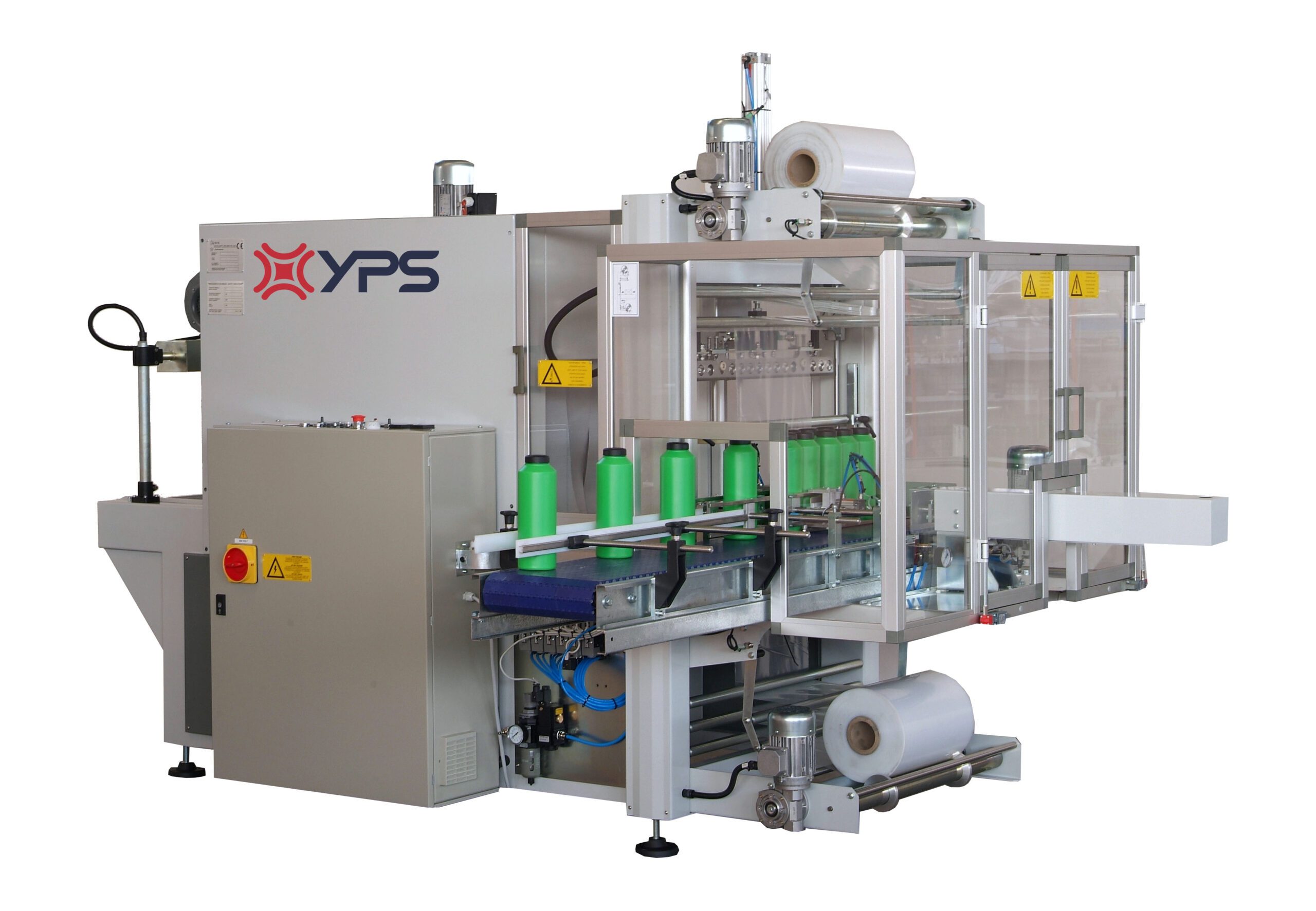
BAMA Compliant specification
Available for aerosol packaging applications.
Simple controls
For total ease of operation. Available as a HMI or switch-based system.
Adaptable infeed
To accept trayed and trayless wrapping applications.
Full perspex guarding
CE marked guarding guaranteeing operator safety but also full line of sight operation.
Low mounted film holder
For easy and safe loading of shrink film reels.
Features & Benefits
Full flexibility
Offers a truly flexible solution. Able to handle trayed or trayless items, singles or multipacks, and even stacked items with ease.
Fast Changeovers
Changeovers between pack types are fast and easy, minimising downtime for the most efficient system.
Labour-Saving
Can be fed either by an operator or directly from a conveyor for a labour-saving option.
Cost-Saving
Comes with a fully recirculated air system, which ensures the most efficient use of heat, keeping costs down while ensuring the best presentation of the finished pack.
For aerosol wrapping, a number of upgraded features can be incorporated.
Ideal specification
Side feed sleeve sealers are available in a choice of three widths to ideally suit your application, operation and factory layout.
Full flexibility
Offers a truly flexible solution. Able to handle trayed or trayless items, singles or multipacks, and even stacked items with ease.
Fast Changeovers
Changeovers between pack types are fast and easy, minimising downtime for the most efficient system.
Labour-Saving
Can be fed either by an operator or directly from a conveyor for a labour-saving option.
Cost-Saving
Comes with a fully recirculated air system, which ensures the most efficient use of heat, keeping costs down while ensuring the best presentation of the finished pack.
Ideal specification
Side feed sleeve sealers are available in a choice of three widths to ideally suit your application, operation and factory layout.
Testimonials
Find out more about Side Feed Sleeve Sealers
Create limitless collations
The side feed sleeve sealer offers you enhanced flexibility in your operation, with the ability to run singles or multipacks, trayed or trayless items and various collations with ease.
Feeding products at a 90° angle to the direction of the shrink tunnel, the side-feed sleeve sealer uses a positive push action to collate products in your desired formats.
If you fulfil a range of different orders, the changeover between products or collations is simple and straightforward, requiring just a tweak of the settings.
A pack clamp is included as standard to deliver complete stability, even for stacked products.
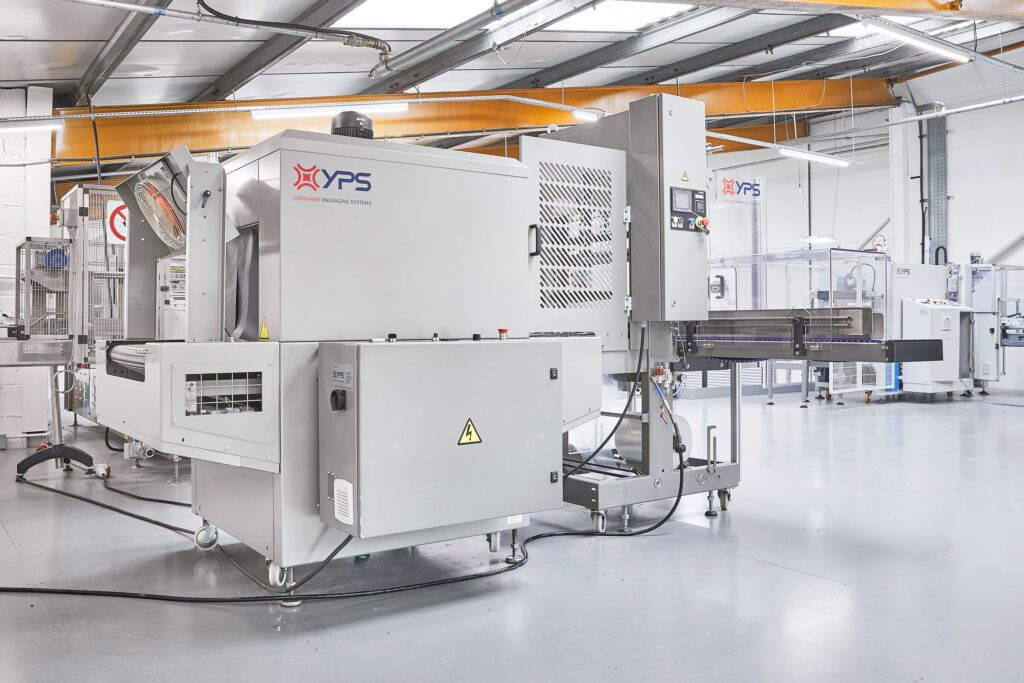
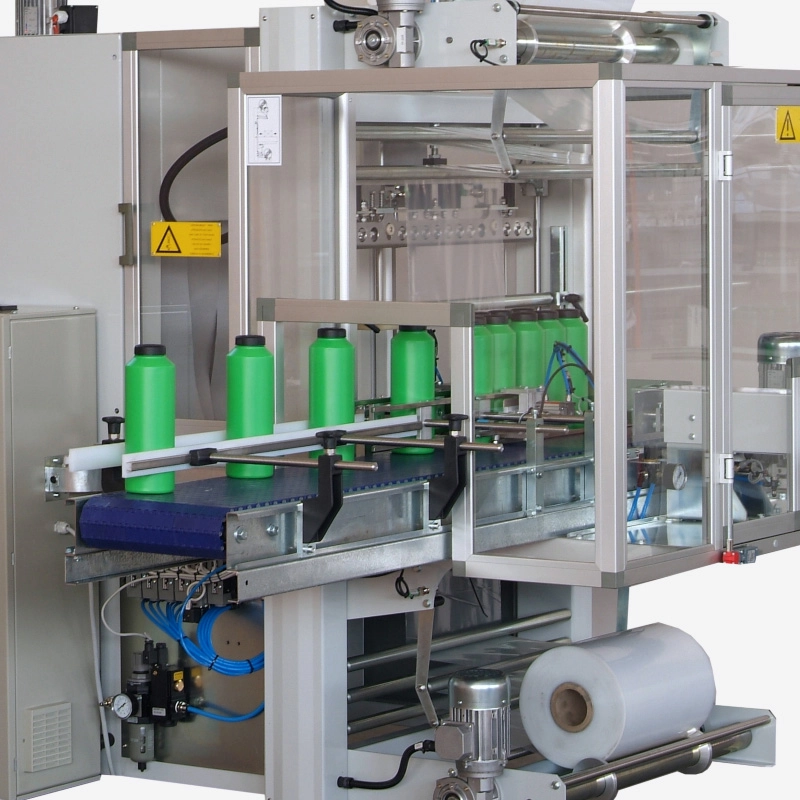
Safety guaranteed
At the end of the infeed belt, a spring-loaded safety plate is installed on the infeed guide to protect the heat sealing machine and packs from damage if for any reason they should jam up or inter-lock due to incorrect setup.
If the pusher plate is narrower than the pack, it typically won’t affect the preceding pack.
However, if a smaller pack is used without adjusting the pusher plate, it could push two packs through the heat shrink film, potentially crushing the preceding pack.
In this case, the safety plate would trigger an automatic shut-down, preventing damage to the machine and packs.
Very few heat shrink sleeving machines on the market have this invaluable feature.
Award-Winning Support
The YPS Team are here to support our customers at every step of their automated packaging journey. Our support is so good that we recently won Automate UK’s prestigious Outstanding Customer Service award.
Our service includes:
- A free service contract with every machine sold.
- Installation and commissioning overseen by our in-house, specialist engineering team.
- Free and unlimited operator training.
- Access to engineering experts out of hours and throughout the year.
- Spare parts for all machines supplied, held in stock at our UK warehouse.
- Extensive stocks of packaging materials, also held at our UK warehouse and available for next-day despatch.
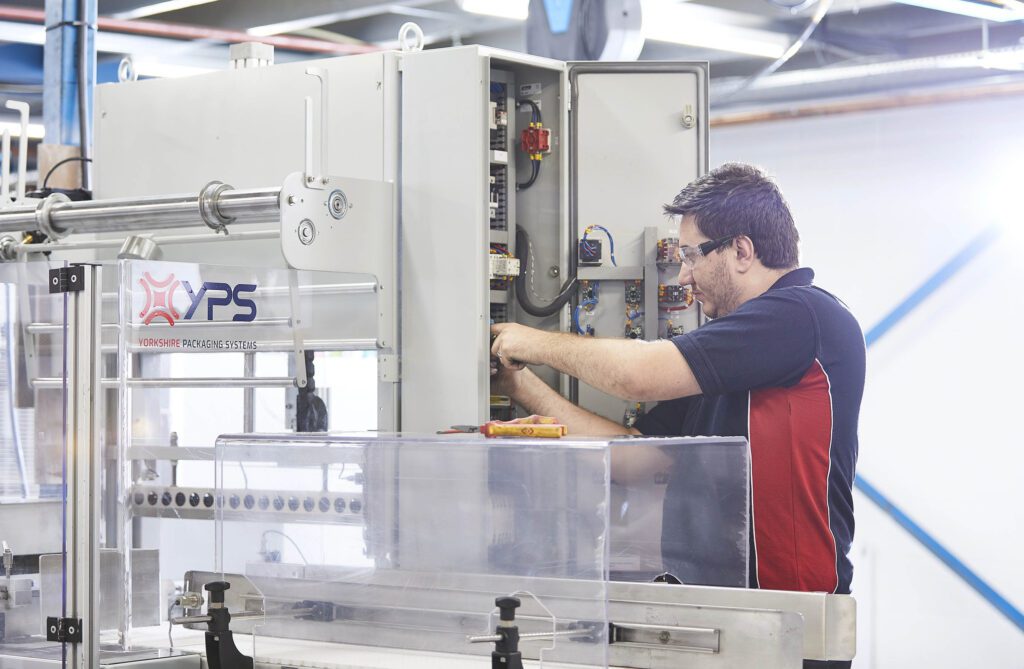
Related machines
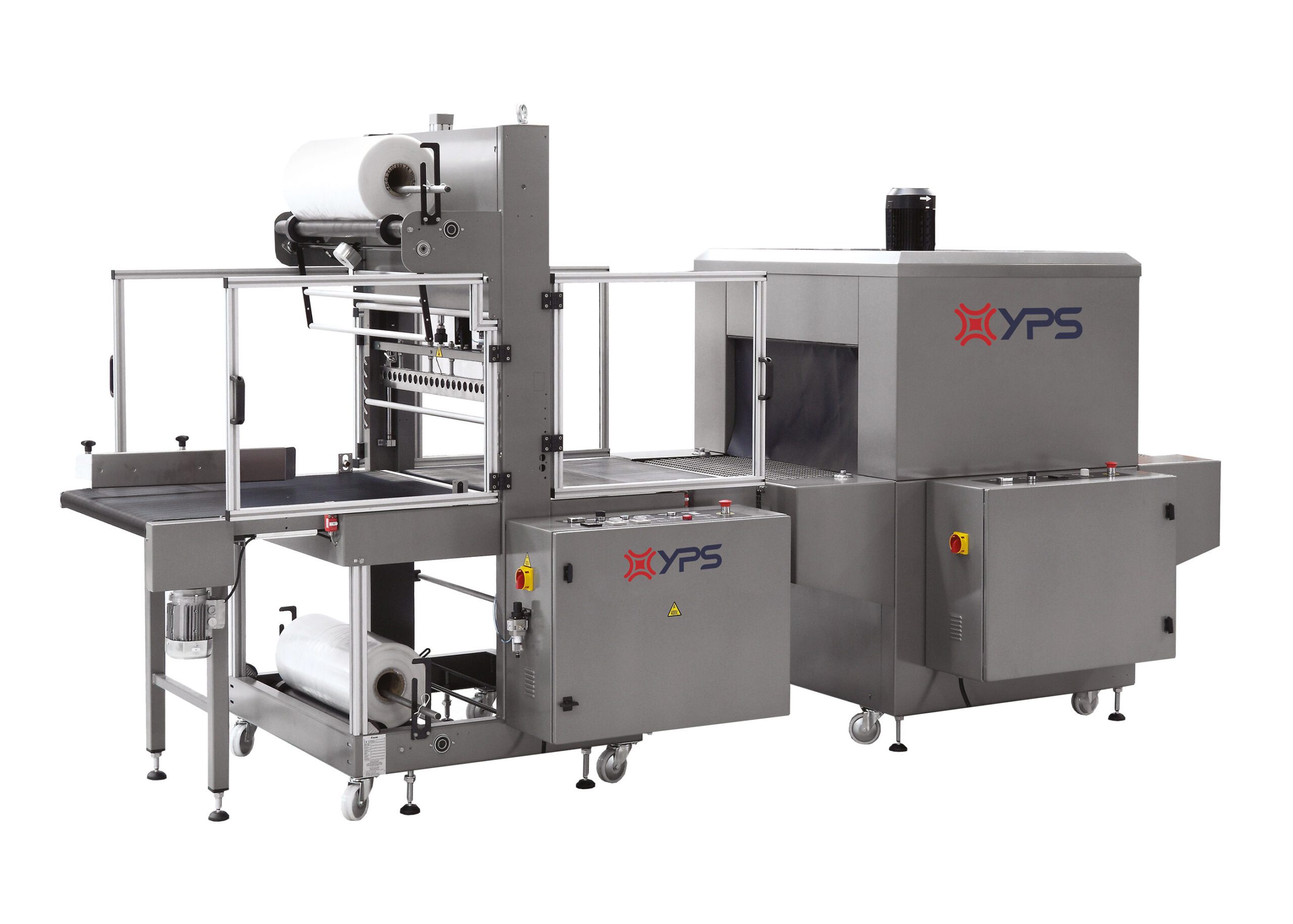
Designed to wrap larger and longer packs, single packs and collations in trays at faster speeds. Simplicity is key with no change parts required between batches.
- Speeds of up to 600 cycles per hour
- Height adjustable sealing jaw for faster production
- Pack clamps for unstable products running at speed
- No change parts required
- Optional kissing conveyor for small packs
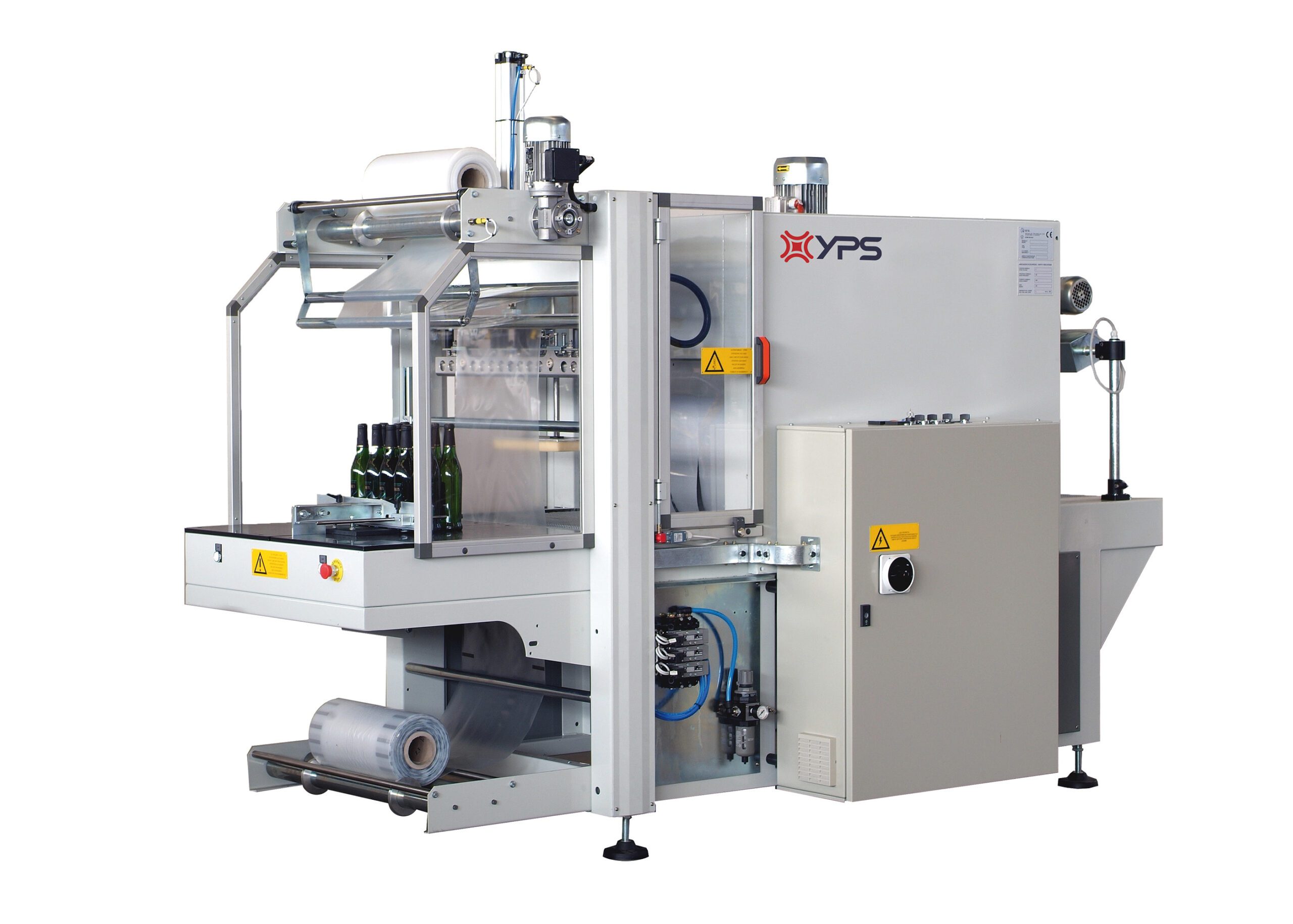
Ideal for low production or low volume wrapping requirements at slower speeds or when using trayless or unstable products where flexibility is key.
- Ideal for unstable packs
- Available as monoblock units or separate sealer and tunnel
- Product packs with or without bullseyes
- Ease of operation
- Heavy duty sealing jaw for consistently strong seals
Get in touch
Reach us directly at 01484 715111, enquiries@yps.co.uk or via the contact form below.
"*" indicates required fields